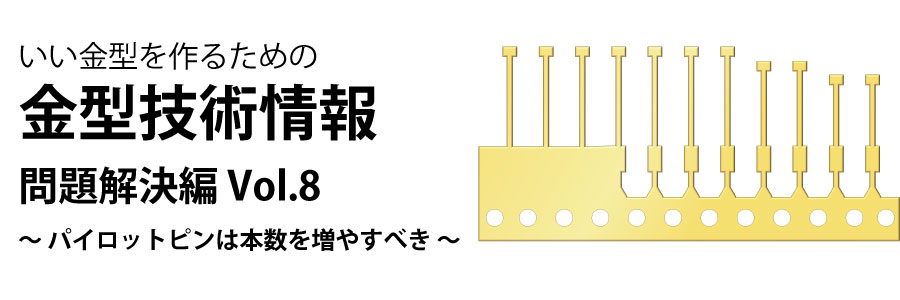
パイロットピンの役割
プレス連続金型には抜き加工、曲げ加工など多くの加工が入り混じった金型が多くあります。
その中にあってストリップレイアウト(被加工材料)の位置決めの重要な仕事を担っているのがパイロットピンとなります。
また、 プレス機械の動きに連動して被加工材料(以後材料と呼ぶ)を1ピッチごと金型内に送り込む役目を担っているのが材料送り装置です。送り装置にはローラー形式であったりグリップ形式など様々なタイプがあります。
ここではパイロットピンがプレス加工のどのタイミングで仕事をしているか、そしてパイロットピンの本数を増やした際の利点について紹介します。
材料送りからパイロットピンの挿入
図-1にあるように、プレス機械のストローク図270°の位置から90°の範囲が材料送りの時間となります。(実際に材料送り作業は160°程度)
この範囲は金型によるプレス加工は全く行われない位置となります。
その後決められた材料送りの仕事が完了し、パイロットピン先端からのパイロット穴に挿入が始まる直前に材料送り装置の材料グリップは解除され、材料は完全にフリーとなり、パイロットピンによる材料位置の微調整(X-Y方向)が行われます。(詳細は以下で説明)
材料はパイロットピンの挿入開始から位置決めが完了して、プレス加工が完了するまでの位置決めは全てパイロットピンの精度に頼っています。
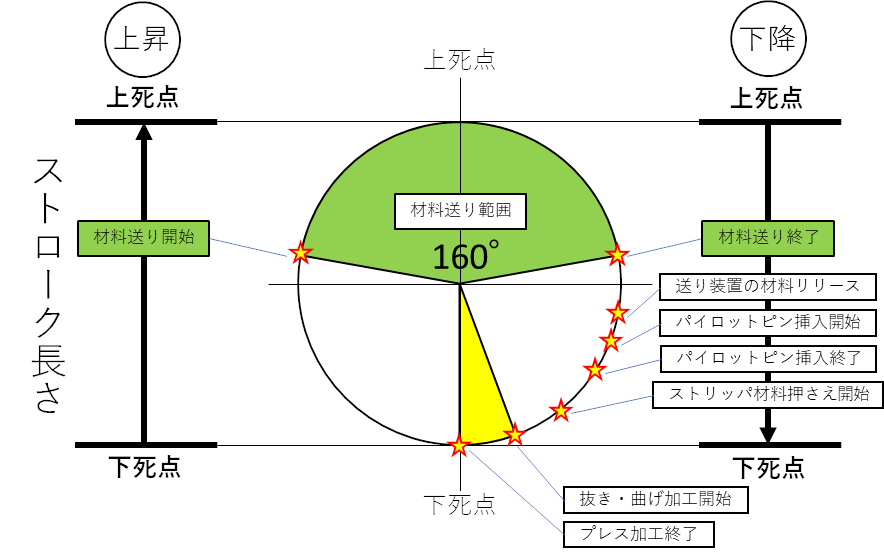
パイロットピンの挿入からプレス加工完了まで
図-2にパイロット穴へのパイロットピンの挿入、そしてリリースのタイミングについて示します。
材料の送りが完了し、パイロットピンの先端(テーパー部)がパイロット穴に挿入が開始されると同時に、送り装置の送りツメが材料のグリップを開放(リリース)します。材料がフリーになり、パイロットピンのストレート部が材料のパイロット穴に挿入されることにより、各プレス加工位置の微調整が完了し、抜き加工や曲げ加工が行われる各工程位置(X-Y方向)に固定されます。
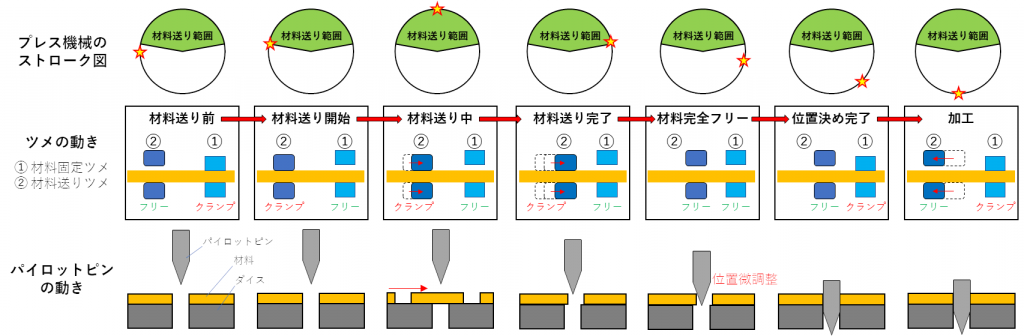
パイロットピンの数はどうあるべきか
ここまで材料送りからパイロットピンによる材料の(X-Y方向)の位置決めを紹介してきましたが、この位置決め(材料位置の微調整)を行うに際し、パイロットピンの数をどうするべきかについて紹介します。
プレス加工のスピード(spm)について
プレス加工のスピードは、いろいろな制約(工程数など)による金型サイズや、材料の板厚や曲げ形状の難易性などにより様々あります。ここではこれらの制約を考慮せず単純に500spmにおけるプレス加工を行う上でのパイロットピンの本数はどうあるべきかについて考えてみます。
500spmの場合の被加工材の位置決め時間について
500spm=1分間にプレス機械は500回の上下運動を繰り返すことになります。
1回のストロークにかかる時間=60秒÷500spm=0.12秒
パイロットピンによる位置決め時間=0.12秒÷4=0.03秒(実施はもう少し短い)
となります。
材料送り装置の精度もかなり高くなっているためパイロットピンによる材料の位置修正量は極微小と考えられますが、この調整を1本のパイロットピンで行うより、図-3で紹介しているように出来るだけ多数のパイロットピンで行うことにより、パイロットピンに与える負担が軽減できるばかりか微調整された被加工材料の位置精度も素晴らしいものとなり、次工程との抜き・曲げ加工関連も精度が保たれます。
多数のパイロットピンを設けることにより加工品の精度もおのずと安定することから、パイロットピンの本数を増やすことをお勧めします。
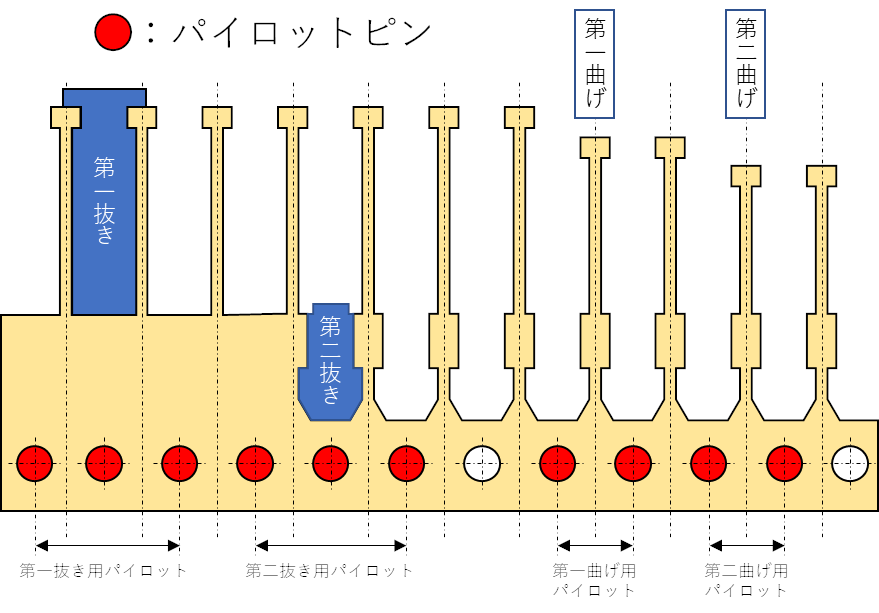