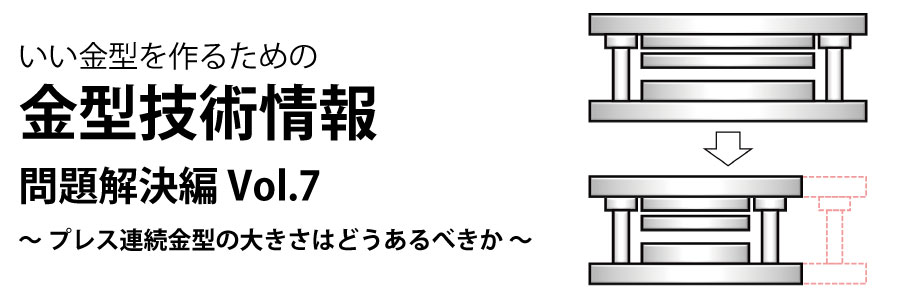
プレス連続金型の大きさ
プレス連続金型において、同じような製品をスタンピング加工(抜き・曲げなど)する金型で、金型の大きさ(長手方向)が異なることをよくお聞きします。
ここでは金型が大きすぎるとどのようなデメリットが発生するか、金型を小さくすることでどのようなメリットが発生するかを実例を踏まえてご紹介します。
プレス加工はストリッパプレートで被加工材料を叩いている
プレス連続金型の場合、1工程目から最終工程まで、そして各工程間に至るまでの間、被加工材はストリッパプレートに毎ショット下死点付近で叩かれていることになります(被加工材料がストリッパプレートにいじめられていると言っても過言ではありません)。
ストリッパプレートは抜きや曲げ加工など工程ごと、そして更に各工程間も被加工材料を押さえています。図-1のように金型のサイズが515mmで送りピッチ1.0mmならば500spmの場合、515回も叩かれていることになります。一方、金型のサイズが小さい320mmの場合、同条件では320回しか叩かれず、約40%減らすことができます。
複雑な曲げ加工や寸法公差の厳しい製品のプレス加工になればなるほど被加工材料に与える外力(回数)は少なくするべきと考えます。そのためにも金型のサイズを小さくすることをお勧めします。
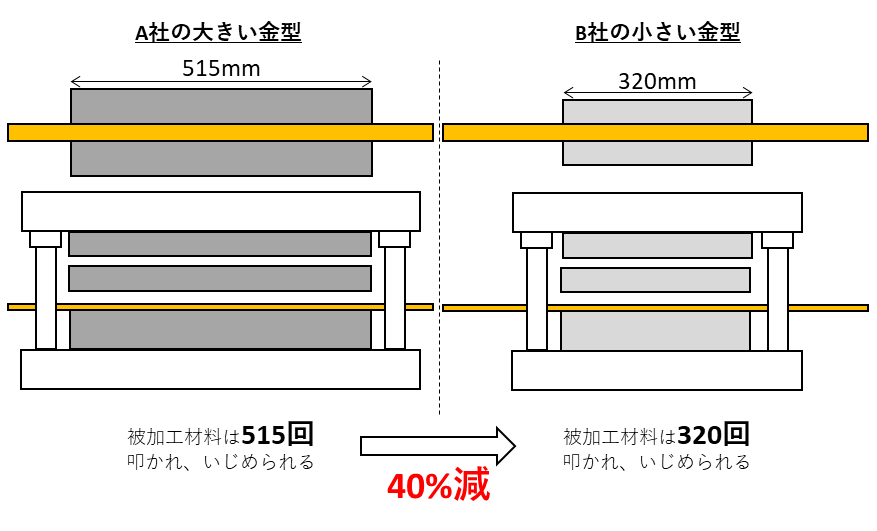
金型の大きさはプレス加工品の精度(寸法・形状)にも影響する
前述のストリッパプレートによる被加工材料の叩かれや抜きによりバリが叩かれることから被加工材料の微妙な蛇行やうねりなどが発生し、製品(プレス加工品)の寸法精度などにも影響を及ぼし、頻繁にメンテナンスを繰り返す金型になってしまうのではないでしょうか。
このように度重なるメンテナンスを行っていると、生産にも品質にも支障をきたすようなってしまうことも考えられます。
大きな金型は高速加工が難しい
大きな金型になると上型の重量も増すことからプレス機械への負担が大きくなり生産スピード(spm)にも影響が出ます。
下表にあるように、大きな金型(515mm)は1200spmに対して小さな金型(320mm)は3000spmでの生産が可能となりました。
ここでの大きな違いは金型の大きさが515mmに対して320mmであり、この違いは曲げ工程の工程数が大幅に異なっていました。それぞれの曲げ工程を比較すると、515mmの金型は31工程、320mmの金型は12工程となっていました。
これは320mmの金型の工程数が単純に少ないため金型を小さくできたのではなく、曲げ構造を駆使(曲げtoolの動きを工夫)して、1工程内での複動曲げや下死点付近でのプレス加工に徹底した構造が特徴の金型であったことと、プレス機械の下死点変動や被加工材料の板厚変動などにも影響されない構造であったことが要因となり、金型を小さくすることに成功しました。
金型サイズ | 加工スピード(実績) | 曲げ工程数 | |
A社 | 515mm | 1200spm | 31工程 |
B社 | 320mm | 3000spm | 12工程 |
大きい金型と小さい金型の生産性の比較
下表に示した生産に関する結果を数値で比較してみると、
生産スピード = 3000spm 対 1200spm = 2.5倍
さらに、
メンテナンス頻度(1回のメンテナンスでの稼働) = 7日 対 2日 =3.5倍
となり、金型を小さくすることにより生産スピード(spm)と稼働状況の向上に結び付いた実例となります。
メンテナンス頻度が少ないということは、製品の品質面でも寸法や形状が安定していることを意味しています。さらにこのような安定した金型であるとメンテナンス作業も容易となり、メンテナンス者の隅々まで行き届いた細やかなメンテナンスが細部に行き渡り、次の生産も安定した稼働ができます。
金型サイズ | 加工スピード | メンテナンス頻度 | |
A社 | 515mm | 1200spm | 1~2日に1回 |
B社 | 320mm | 3000spm | 1週間に1回 |